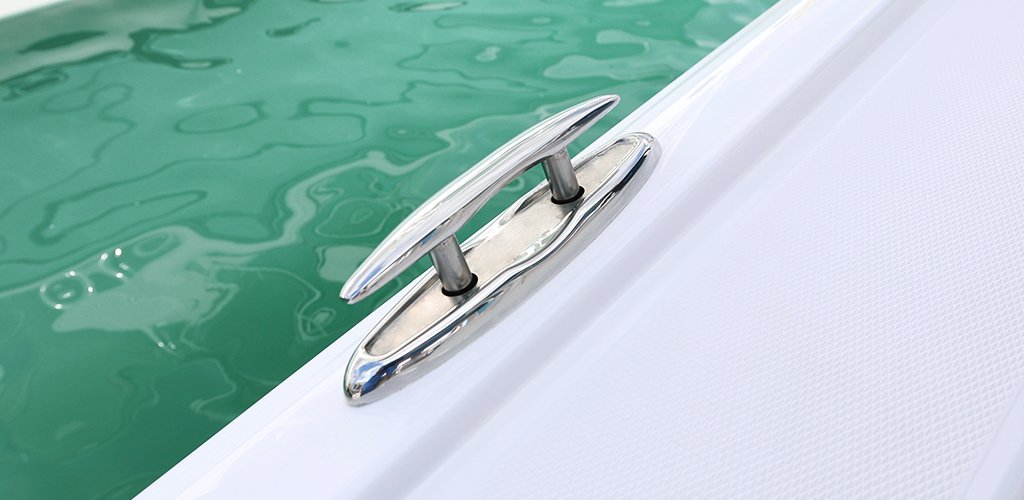
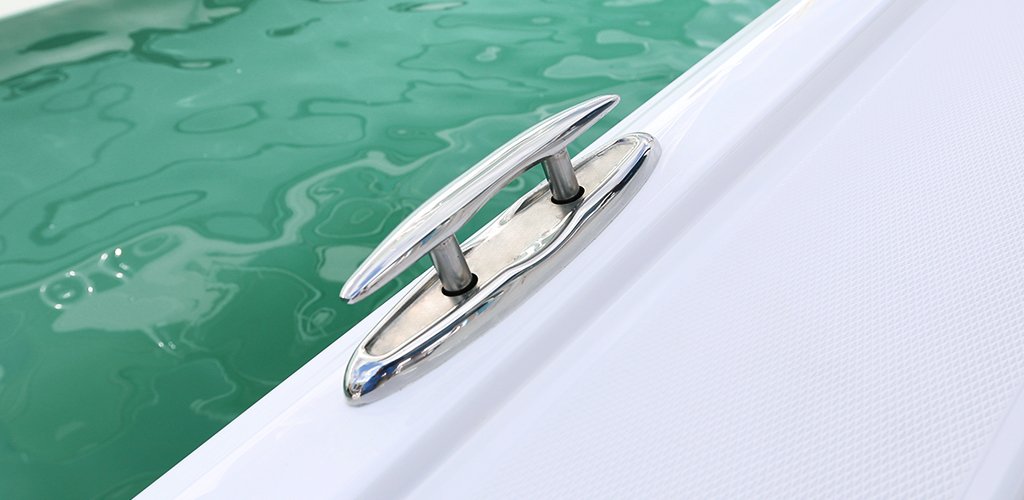
The Gemlux Advantage
Electropolishing
Electropolishing, in its broadest definition, is a process which brightens, deburrs and passivates stainless steel. GEMLUX® electropolishing is different because it consistently achieves a bright, uniform finish. Scientific methods are utilized to assure the electropolishing solution remains VERY stable. Unlike many others who treat electropolish as an art, GEMLUX® electropolish is considered a science.

The “E.P.” Process
Chromium, which is a component of stainless steel, is electrochemically enhanced on the product surface. The chromium-to-iron ratio on the surface of the stainless steel is transformed through iron removal from a 1:6 to a 4:1 ratio. The chromium oxide layer that is formed is a homogeneous constituent of the metal. It cannot delaminate or peel and is extremely corrosion resistant.
A stainless steel piece is placed on a copper rack and immersed into an electrolytic acid bath. This proprietary GEMLUX® bath consists primarily of phosphoric and sulfuric acid. The bath temperature may range from 120° - 180° F. Electricity is run through the rack (the anode) and the work part pieces. At this point, the negatively charged cathodes draw the iron off the surface of the stainless steel.

In most electropolishing solutions, the iron ions are dissolved into the acid solution or dumped to the bottom as sludge, and as the iron builds up, quality and consistency decrease. This does not happen with GEMLUX®. We actually plate the iron to the negative cathode and remove the contaminating iron on a daily basis. This produces a consistent finish on each stainless steel product.
Some Technical Details
The corrosion of stainless steel is counteracted by passivation. Without passivation, iron or iron oxide exists on the surface of stainless steel. When any machining or fabrication operations are performed, the condition is worsened. Aside from iron being deposited by tooling, it is also being entrapped underneath the “smeared skin” created by the mechanical operation. This is why GEMLUX® processing is so valuable.
Surface passivation by nitric acid immersion only attacks iron at the surface. This only partially solves the problem. The remaining iron under the skin will now corrode both inwardly and outwardly. The inward corrosion is known as I. G. A. or intergranular attack. The results are metal fatigue and surface corrosion. Any applications requiring a clean environment such as gas or liquid valves and pumps, bearings, vacuum systems, or fuel supplies would be subject to detrimental effects without thorough passivation.
GEMLUX® processing resolves this problem entirely. Surface contaminants and the false skin which entraps iron are removed electrochemically. The surface that remains after processing is positively the cleanest, most passive surface possible. The microfinish is lowered and dimensions with close tolerances do not pose a problem. The rate of metal removal is controllable with this process.